Magnetic DRO Scales
Introduction
Magnetic scales are a form of linear quadrature encoders that use a magnetized strip with precisely spaced poles to read the position. Since the strip often has adhesive backing, it's more commonly referred to as magnetic tape. The reading head contains a sensor that can detect changes in magnetic field and convert it to precise position data.
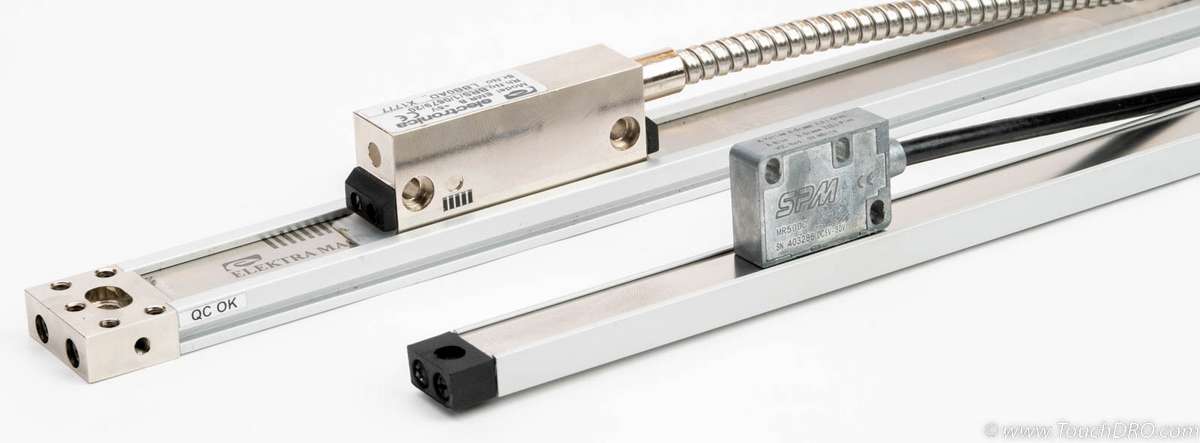
Principle of Operation
Magnetic quadrature encoders are much more complicated devices compared to the optical encoders use in Glass DRO Scales. While they possess some properties that are very desirable for digital readout application, they also have some serious drawbacks. In order to understand the tradeoffs of using magnetic scales in a DRO, it's important to have a good grasp of how these scales work.
Magnetic Tape
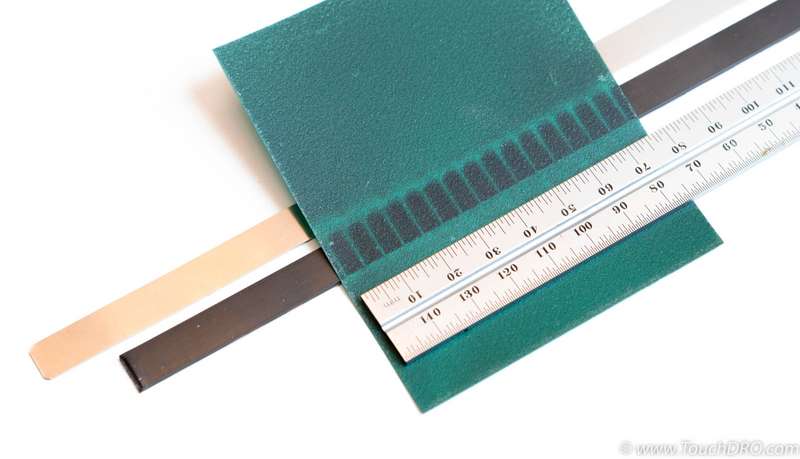
Magnetic tape used in these scales is made of ferromagnetic powder that is held together by rubber-like binding agent and is magnetized in a way that produces series precisely spaced poles running perpendicular to the long dimension. Common scales use tape with pole-to-pole distance ranging from 1mm to 10mm.
The Sensor
A (or the scales) scale works by detecting a change in magnetic field and converting it to distance. The most common type of magnetosensitive device used in magnetic scales is a Hall effect sensor. This type of sensor can detect the presence of static magnetic field. It employs a thin strip of metal with a small current applied to it. In the presence of magnetic field, the electrons are deflected towards one side off the sensor producing small voltage across it that is proportional to the strength of the magnetic field. For instance, the voltage can be the highest when the sensor is right over the North pole and the lowest when it's over the South pole, or vice versa. As the sensor moves along the scale, it produces sinusoidal waves with periods identical to the space between magnetic poles.
Interpolation Circuit
In order to achieve resolution on the order of microns, magnetic DRO scales use two sensors spaced so that the waves are offset by a very small amount, producing what is commonly known as a sine/cosine output. The scale can then use one of several different interpolation algorithms to convert the instantaneous difference in amplitude between the sine and cosine waves into a square wave output. The period of the resulting wave is equal to the Arctangent of the ratio of sine to cosine voltage.
There are several ways this interpolation is implemented, but most modern high-resolution DRO scales use either Vector Tracking Conversion or Continuously Sampling A/D Conversion.
- Vector Tracking Conversion offers lower cost, good resolution and real-time response since there is no digital processing involved but has no error correction. This conversion method is preferable in high-speed motion control systems where responsiveness is more important than precision.
- Continuously Sampling A/D Conversion uses continuously-operating A/D converters with digital processing to calculate the position. Due to the signal processing, these converters can achieve much higher resolution, a perfect 50% square wave with virtually no jitter and excellent error correction. The tradeoff is the higher cost and introduction of slight delay on the order of several microseconds. As a result, this method is less suitable for motion control systems but is preferable for DRO applications.
Sources of Error
Magnetic DRO scales are inherently more error prone than glass scales since they work by interpolating analog signals derived from changing magnetic field. Imprecise magnetic tape, mounting errors and thermal drift in the conversion circuit are the most common ways to introduce position error:
Imprecise Magnetic Tape
In order to achieve optimal accuracy, the sensor needs to produce sine/cosine waves that are as close to ideal as possible with constant phase offset. Magnetic tape that is not precisely magnetized can have the following defects:
- Non-uniform magnetic pole spacing that will result in sine/cosine waves that have varying period and phase offset
- Non-uniform magnetic field strength between the poles that will affect the amplitude of the waves
- Non-uniform ferromagnetic powder distribution with result non-uniform magnetic field that will affect the Voltage difference between the waves
These defects introduce interpolation anomalies that result in non-linear position error. The result is very similar to how a glass scale with uneven encoder etching would behave.
In practice, the quality of the tape is the single largest predictor of the overall accuracy of the magnetic scale. High quality tape is relatively expensive to produce since it needs to have very uniform size and distribution of magnetic particles and the magnetization process that is very exacting. As a result, tape quality is the area where budget magnetic scale manufacturers cut cost, using lesser quality substrate and less precise magnetization process.
Uneven Tape-to-Sensor Distance
The strength of the magnetic field is inversely proportional to the square of the distance between the source and the sensor. In other words, as the distance doubles, the field strength dops by a factor of four. There are three scenarios that can affect tape-to-sensor distance.
- If the tape is not precisely flat as a result of uneven mounting surface or nonuniform thickness, the distance will fluctuate at relatively small scale. This produces the same effect as unevenly magnetized tape described above.
- When a tape is not mounted precisely parallel to the plane of reading head travel, the distance between the head and the tape will be larger on one end than the other. As the sensor travels across the scale, the strength of the magnetic field decreases and signal-to-noise ratio drops, resulting in growing interpolation error and jitter. Additionally, this introduces linear cosine error.
- Finally, if the horizontally-mounted tape is supported only by the ends, it will have some amount of droop that will result in large distance in the middle compared to the ends. The result will be very similar to the above, but the error will be non-linear.
While the latter two issues can be addressed by adding adequate support and careful aligning the scale, the first issue is much more tricky to deal with. Furthermore, the rubber used in the magnetic strip has coefficient of thermal expansion that is one or two factor of magnitude larger than that of cast iron, so temperature fluctuation in the shop can affect scale flatness.
Measurement Error Due to Imprecise Conversion
Both the magnetosensitive devices in the reading head and the semiconductor devices involved in position interpolation are sensitive to temperature fluctuations. For example, the comparator circuit used by Vector Tracking method and the converter used by the Continuous Sampling Analog-to-Digital method rely on accurate voltage reference. All real-life voltage reference devices exhibit some amount of temperature drift that can translate to conversion error over time.
High-end scales use more sophisticated [and therefore more expensive] electronics with built-in temperature compensation that can work around the thermal drift and achieve very accurate reading across a range of temperatures. For the less expensive scales, this is another area where the manufacturers can cut some cost, so their accuracy and repeatability is nowhere near as good.
Pros
Small Form Factor
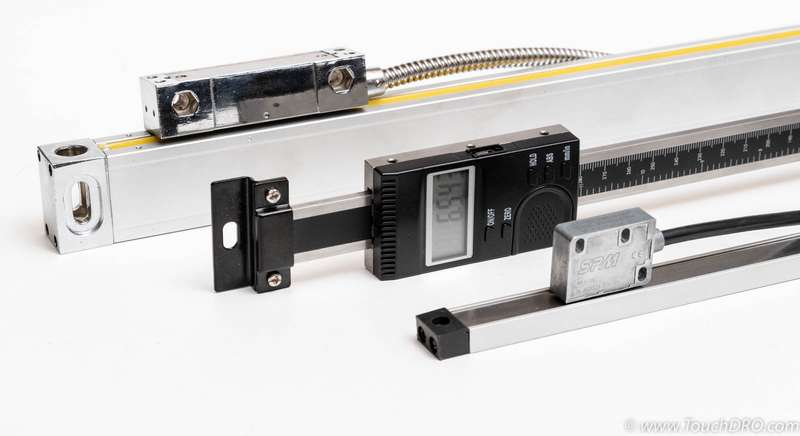
Unlike glass DRO scales, magnetic scales don't have to be enclosed in bulky casing. This, in conjunction with a smaller reading head, means that these scales have by far the smallest form factor among the DRO scales. As a result, magnetic scales take up much less space on the machine and can be used in very tight quarters.
No Length Restriction
Since magnetic tape can be produced in a continuous roll of very large length, magnetic DRO scales have practically no upper size limit and can be used on machines with hundreds of meters of travel. Conversely, the scales are very easy to cut to needed length making them ideal for smaller machines.
Excellent Long-Term Durability
Magnetic DRO scales have no internal moving parts and the reading head [usually] doesn't come in contact with the encoder strip. Consequently, there are no mechanical parts that can wear out and fail. Similarly, thanks to the inherent durability of modern semiconductor devices, the electronics have excellent reliability as well. As a result, magnetic scales have unparalleled long-term reliability and can last for many decades without any issues.Cons
Sensitivity to Misalignment
As discussed earlier, magnetic scales are very sensitive to misalignment since any misalignment decreases sensor voltage amplitude and, as a result, creates unfavorable interpolation conditions. In order to achieve optimal performance, the reading head has to be mounted as close to the surface of the magnetic tape as possible without touching it. Furthermore, the scale has to be mounted precisely parallel to the plane of axis travel and the head has to be exactly parallel to the scale. While the scales can tolerate small amounts of misalignment in any direction, their performance degrades rapidly resulting in conversion errors and jitter that can ruin the accuracy of the digital readout.
Sensitive to Ambient Temperature
Magnetic scales are much more sensitive to temperature fluctuations than other DRO scales. There are two main reasons for this. First of all, the tape uses a rubber-like binding agent that has a relatively large coefficient of thermal expansion compared to most metals. The tape is usually sandwiched between rigid metallic mounting surface and thin strip of stainless steel. Since the tape has thermal expansion coefficient at least a factor of magnitude larger than the underlying metal substrate, it can cause localized warping and resulting nonlinear errors. Second, interpolation circuit can be affected by thermal drift of the voltage reference unless the circuit has proper temperature compensation provisions.
For comparison, gray cast iron would expand by about 0.0057" over 48" with 20F temperature change; glass would expand by 0.0048", hard rubber would expand by 0.048" and even one of the most dimensionally plastics, PEEK would expand by about 0.042".
Sensitive to Ferrous Dust and Swarf
Since the tape used in magnetic scales is quite obviously magnetic, small ferrous particles such as grinding dust of small metal chips are attracted to it. When they get in between the tape and the reading head, they cause small distortions in the magnetic field that can interfere with the accuracy of position interpolation.
Quality vs. Price Considerations
Until a decade ago, high-end scale manufacturers such as Sony Magnescale and Newall dominated the magnetic DRO scale market. More recently, EMS (Electronica Mechatronic Systems) started offering less expensive magnetic scales and heavily marketing them for general purpose digital readouts. Over the last few years, inexpensive Chinese magnetic scales started appearing on the market making them an appealing choice for DRO use.
When comparing magnetic DRO scales, it's important to understand that there is huge performance, accuracy, and quality gap between the high-end Sony or Newall scales, mid-range EMS scales, and budget Chinese scales.
The accuracy and repeatability of magnetic scales is determined by the quality of the magnetic tape and the interpolation electronics. High-end scales use very precise and uniform tape, and much more sophisticated and accurate electronics. Mid-range scales are able to cut the cost by using less expensive encoder strips and simpler electronics, but in general, offer performance that is adequate for the majority of machine shop applications. Low-end Chinese scale manufacturers are able to hight the incredibly low price by using very low quality tape and cheap electronics that lack temperature compensation, proper conditioning circuit or error correction.
Conclusion
Magnetic DRO scales offer properties that make them very desirable in some DRO applications but due to the higher complexity of the interpolation mechanism these scales have some notable drawbacks. Traditionally, magnetic scales were seldom used in mainstream digital readout models and were mostly relegated to specialized applications. They shine in situations where extremely long axis travel was required or where space to mount the scales is limited. As more reasonably priced scales were introduced by manufacturers such as EMS (Electronica Mechatronic Systems), magnetic DRO scales have become more common. When shopping for magnetic scales, it's important to remember that good scales cost real money and inexpensive scales are able to hit the price point by cutting corners.